Technological line of pipe repair
S = 700м2
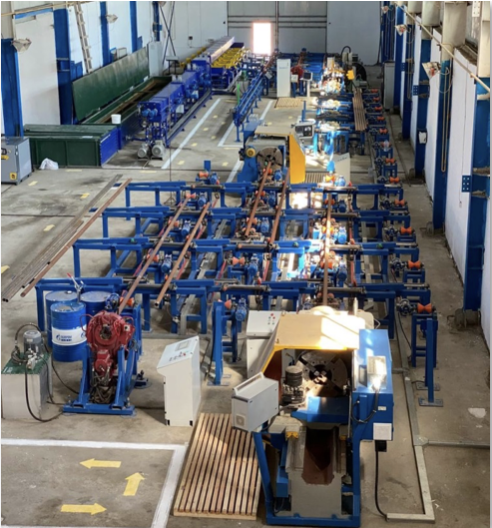
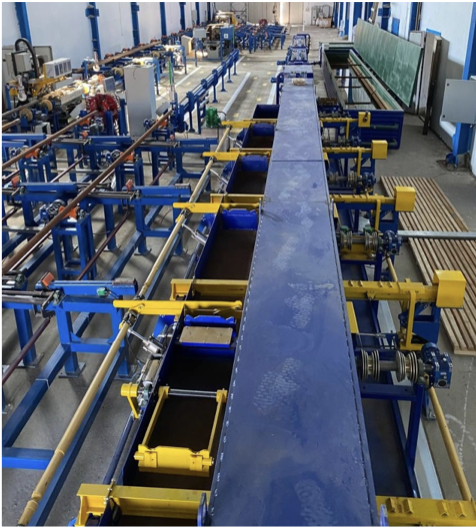
The technological line is designed to carry out comprehensive diagnostics, repair of used pipes, as well as finishing processing of tubing and casing pipes using modern technologies and methods on high-performance equipment; The technological process for repairing tubing and casing pipes complies with the requirements of GOST 633-80, GOST 632-80, GOST 31446-2017; API 5 CT; Processed pipes diameter 60-168mm; Line capacity up to 35 pipes per hour. (depending on size).
Technological process of pipe repair
- Hydromechanical cleaning of the outer and inner surface of pipes – automated washing complex;
- Gauging the inner cavity of pipes with a cylindrical mandrel – installation of electromechanical gauges;
- Mechanized lapel of couplings – machine for screwing and unscrewing pipes “BIZON”;
- Non-destructive testing of the body and ends of pipes with sorting by class depending on the remaining wall thickness – ultrasonic installation for testing the body and ends of pipes;
- Thread cutting – pipe-cutting machine with numerical control;
- Turning couplings with a given torque – a machine for screwing and unscrewing pipes “BIZON”;
- Hydraulic testing of tubing and OT with pressure up to 70 MPa – installation of hydraulic testing of pipes;
- Marking of tubing and OT by impact method and packaging of pipes – Installation of marking “TELESIS”;
Automated pipe washing complex
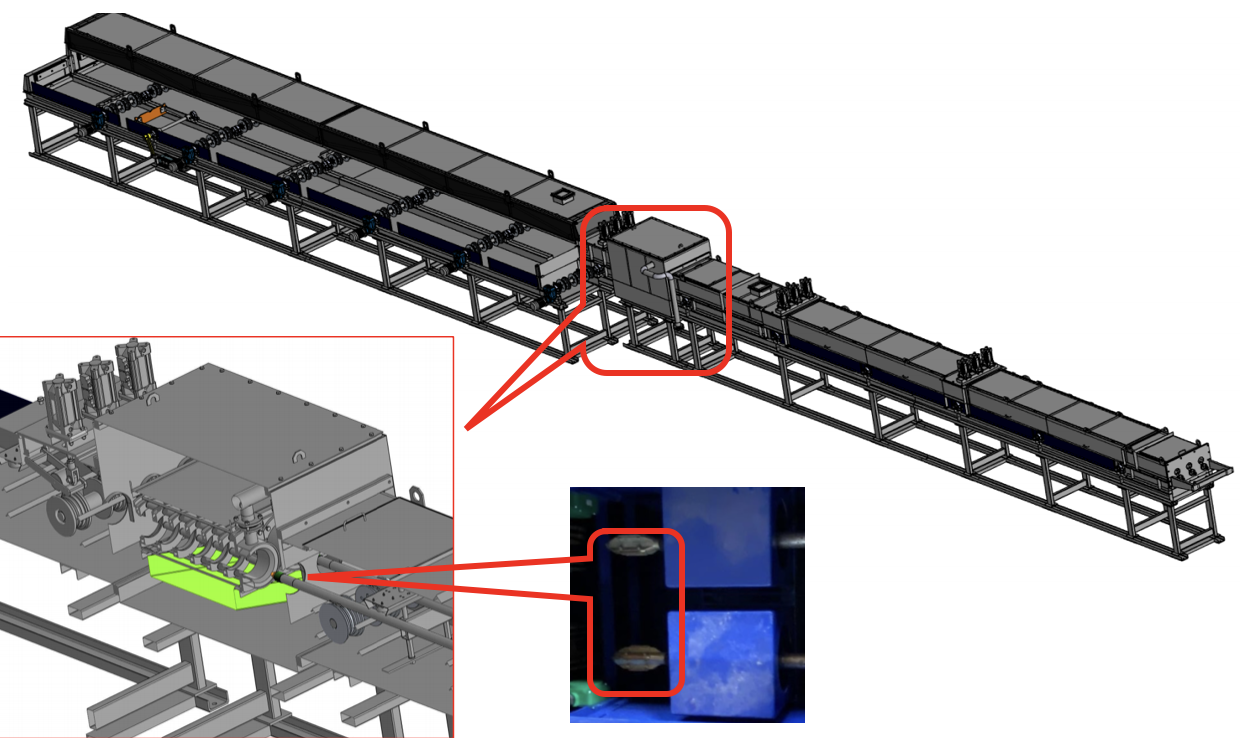
-Translational-rotational movement of heads with hard-alloy knives with simultaneous supply of cleaning solution provide high quality cleaning of the inner cavity of the pipes;
-Seven contours of external washing completely cover the outer surface of the pipes
-Water treatment system includes bath with activators for hot tubing cleaning
Automated template installation
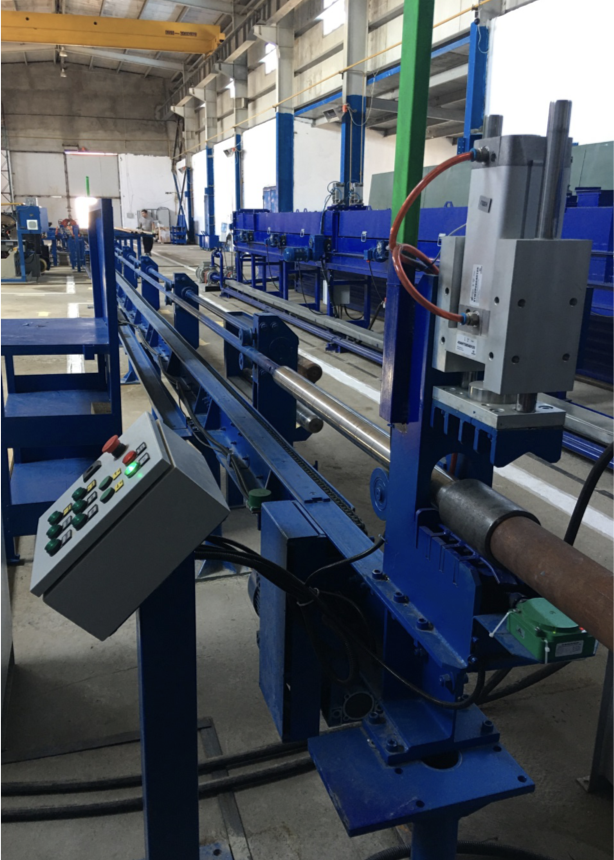
The installation design provides the following parameters:
-checking the internal cavity and curvature along the entire length of the pipe with a cylindrical mandrel 1250 mm long in accordance with GOST 633-80, GOST 31446-2017;
-alignment of the cylindrical mandrel relative to the pipe;
-quick changeover to various standard sizes;
– protection against jamming of the mandrel in the inner cavity of the pipe;
Nominal pipe diameter, mm | Wall thickness, mm | Mandrel outer diameter, mm |
60 | 5,0 | 47,9 |
73 | 5,5 | 59,6 |
7,0 | 56,6 | |
89 | 6,5 | 72,7 |
8,0 | 69,7 | |
102 | 6,5 | 85,4 |
114 | 7,0 | 97,1 |
Automated installation of ultrasonic testing of body and pipe ends
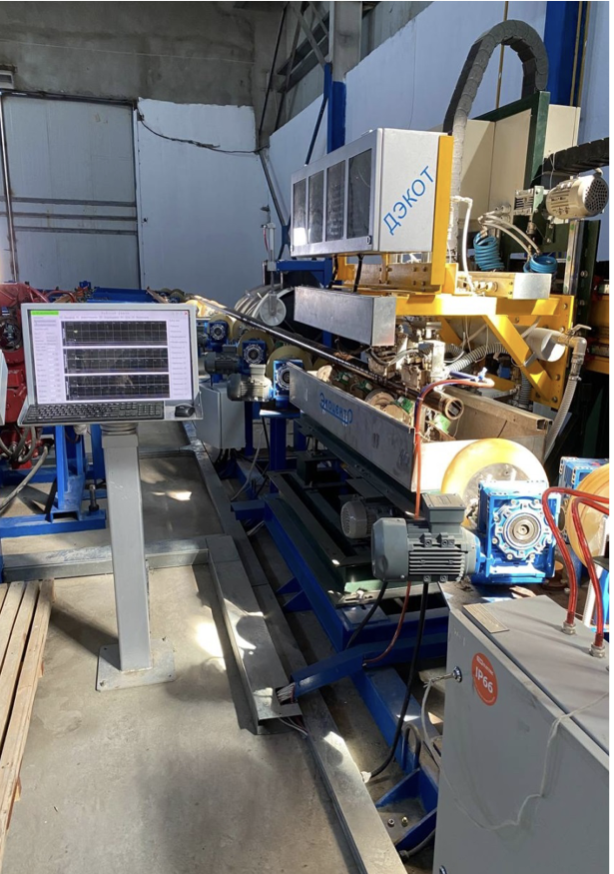
Purpose and effective scope:
The ultrasonic control system is designed for automated measurement of wall thickness, detection of longitudinal and transverse defects of metal pipes in the technological flow of repair and metallurgical production.
Advantages:
- a wide range of controlled pipes 60-168mm;
- the system provides control of the body and pipe ends;
- when inspecting threaded pipes, a program-defined indent for the length of the thread is provided;
- there is no need to reconfigure mechano-acoustic systems when switching to another pipe size;
- recording the results of control, with the formation of a database;
- The system is entered in the State Register as a means of measurement, has a verification certificate;
Automated installation for flaw detection and pipe coating control
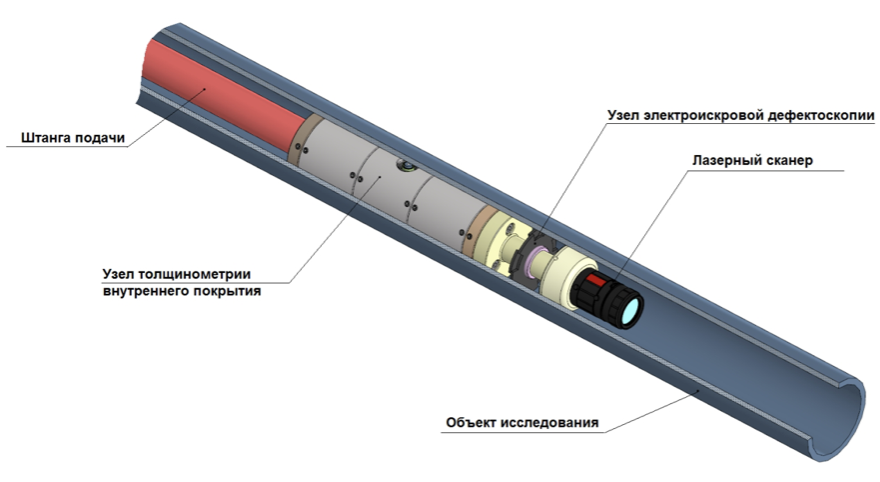
The installation includes the following modules:
- Electrospark flaw detector
- thickness gauge
- Machine vision system
- {Analytics with software
The main functionality of the complex:
- Carrying out electrospark flaw detection of the inner surface of pipes
- Measurement of the thickness of the inner coating of pipes
- Conducting a video inspection of the inner surface of the pipe using a machine vision system
- Identification and measurement of geometric parameters of defects in coatings and base metal present on the outer and inner surfaces of pipes
- Controlled pipe diameter range: from 50-1420 mm
Thread cutting section
CNC pipe-cutting machines provide cutting of any types of threaded connections for tubing and casing pipes in accordance with GOST 633-80, GOST 632-80, GOST 31446-2017, API 5 CT
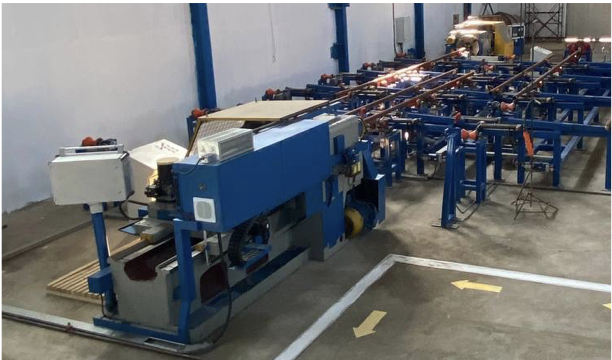
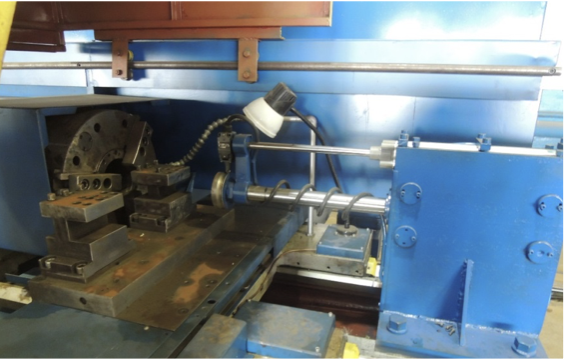
Special types of threaded connections for casing and tubing
high strength
Gas tight (premium tubing)
Sleeveless casing
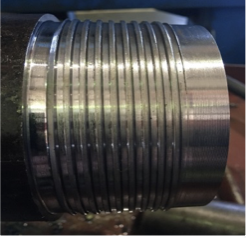
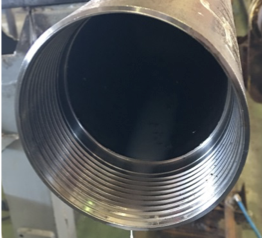
Tubing hydraulic testing area
Automatic rejection of tubing according to the results of hydraulic testing.
Collection of test results for each tubing by videographic recorder “Metran 910”
Advanced heads for high performance
Automatic rejection of tubing according to the results of hydraulic testing.
Collection of test results for each tubing by videographic recorder “Metran 910”
Transport system
Advantages of the transport system:
- To reduce the noise level, racks for the piece supply of NK were used
- No tipping of pipes and risk of damage to threaded parts
Certification
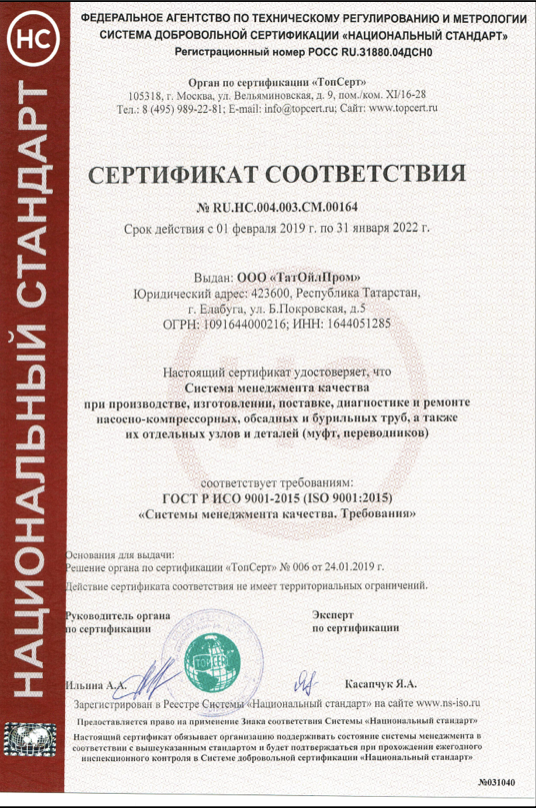
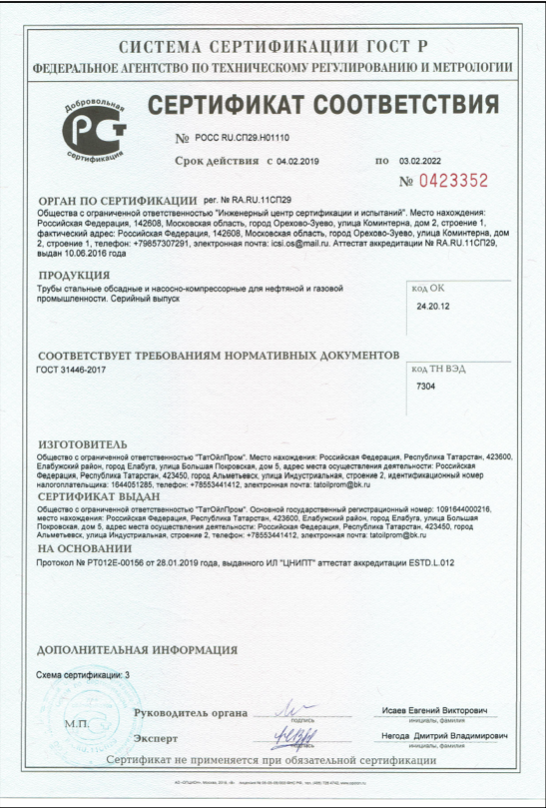
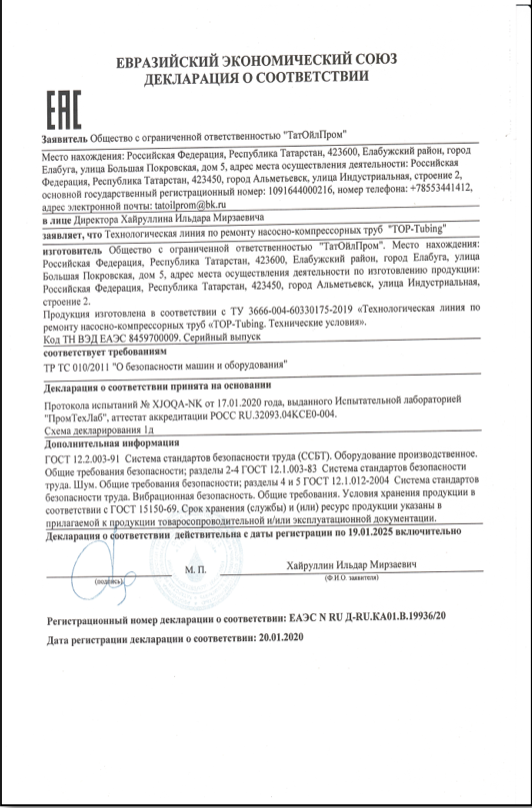